Classic Shock Vibration Testing
Single Axis Shaker Vibration Testing
The Classic Shock vibration testing system provides precise, real-time, multi-channel control and analysis for time domain transients. Pulse types include half-sine, haver-sine, terminal-peak sawtooth, initial-peak sawtooth, triangle, rectangle, trapezoid.
Up to 8 channels for control, alarm checking on master module
Up to 511 channels for monitoring and time data recording
Built-in MIL-STD-810 alarm/abort profiles
Shock response spectrum analysis for input signals
Classic Shock Control
Control Parameters
- Sampling Rate: up to 102.4 kHz
- Time Block Size: 512 to 65,536 points
- Average Number for Control: 1 – 4
- Test Start Method: pretest runs with four excitation types: positive pulse, negative pulse, Random with close-loop control, Random with open loop.
Measured Signals and Display Status
- Measured Signals: drive signal, input time stream, drive signal spectrum, system transfer function, high abort, low abort, control signal, profile, strip chart plots for the time history of RMS, Peak, Peak-Peak level of each channel.
- Display Windows: control composite, signal plot window, signal value window, digital I/O view window, runlog window, large numerical value display window, channel status window, recording status, run schedule, Lissajous plot, vibration visualization, cross plot
- Runlog: a test log continuously records real-time status changes and user commands.
Unique Features in Classic Shock Vibration Control
Vibration Visualization: The EDM Vibration Visualization feature is available in EDM VCS software all test types, including MIMO VCS. This option provides fast and efficient structural model generation and full 3D visualization of the online vibration pattern on the structure under test.
Multiple instances of EDM VCS can run simultaneously on the same computer. Each instance connects a Spider system to run the vibration controller software. All instances must run different tests. This feature provides a central place to control multiple Spider systems and perform vibration tests separately.
Black Box Mode: Operating Without a PC
A supported front-end can operate in Black Box mode which allows it to perform a test without a connected PC. In this mode, a PC is used only to configure the system before the test and then to download the data after the test is complete.
Multi-shaker control (MSC) is a unique feature offered enables users to view and monitor multiple shaker tests from one PC station. Up to 12 controllers can be accessed simultaneously.
Reference Profile and Run Schedule
- Test Standards: MIL-STD-810G, MIL-STD-810H, MILSTD-202F, ISO 8568, IEC 60068, User-defined
- Shock Wave Types: half-sine, haver-sine, terminal-peak saw tooth, initial-peak saw tooth, triangle, rectangle, and trapezoid
- Compensation Shapes: half-sine, rectangular, double rectangular, rounded-rectangular or displacement optimum
- Compensation Locations: pre-pulse, post-pulse, or prepost compensation
- Run Schedule: a schedule includes unlimited number of pulse entries and user-defined events
Vibration Utilities App
Crystal Instruments in partnership with our sister shaker company Sentek Dynamics provides users with the Vibration Utilities mobile app on iOS and Android. This app provides calculation features for sizing your vibration profile (Random, Sine or Shock) and searches through our catalogue of shakers and controllers for the best fit.
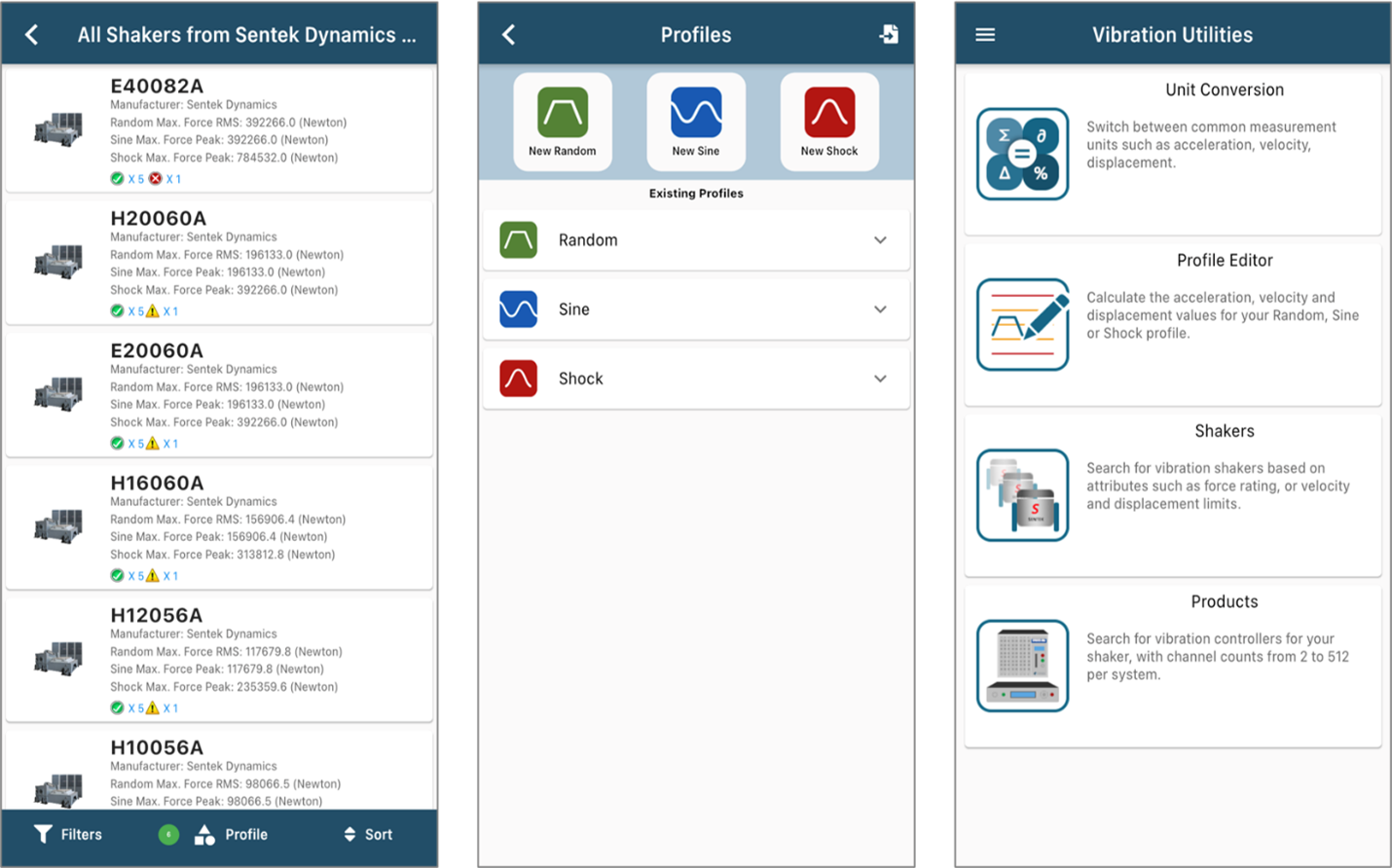


Continuous Data Recording
During vibration testing, all measurement input and drive signals can continuously record to a Spider-NAS or the internal storage residing in each front-end. Users can view and analyze data files with Crystal Instruments Post Analyzer. The variable sampling rate can be enabled to simultaneously record slow-change signals together with high speed vibration data.
Spider Vibration Testing Hardware
A Spider system can consist of one or more Spider hardware front-ends. The user constructs the system by combining Spider front-ends detected on the same LAN. The software validates and displays hardware attributes of each Spider front-end. The following hardware is supported by EDM VCS software for vibration testing, monitoring, and data acquisition.
- Spider-81/81B Vibration Test Controller
- Spider-80Xi High Channel Vibration Test Controller - Scale up to 512 Channels
- Spider-80X Dynamic Measurement & Vibration Control System
- Spider-80M MIMO Vibration Test Control System
- Spider-80SG General Data Acquisition Device with Strain Measurement
Related Vibration Testing Software Options
- Transient Time History Control (TTH)
- Transient Random Control
- Shock Response Spectrum (SRS) Synthesis & Control for Vibration Testing
- Earthquake Testing Control for Seismic Vibration Testing
Monitoring Through EDM Cloud
All vibration tests in EDM-VCS support status checks through EDM Cloud. With EDM Cloud support, users can set up any VCS test to upload live data or run logs for completed tests to a cloud storage space provided by Crystal Instruments, where data is securely stored in the user’s account.
The EDM Cloud website is located at https://cloud.go-ci.com. Users can access EDM Cloud from anywhere in the world to check the status of past and current tests. A secure login flow ensures the status can only be checked by authorized personnel with proper credentials. Multiple logins for accessing the same Cloud account is available.
|
|
|
|