Accelerated Vibration Testing using Fatigue Damage Spectrum
Accelerated Vibration Testing using FDS
Accelerated vibration testing uses Fatigue Damage Spectrum (FDS) to compare the potential damage caused by different Random and Swept Sine profiles. In a similar fashion to Multi-Sine Control, FDS provides a way to reduce testing times by calculating the quickest path to destruction or damage. Testing times are accelerated by focusing random or swept sine energy, depending on the FDS calculation, to where it will induce the most fatigue.
Click to enlarge - Accelerated Vibration Testing using FDS
Generate the random profile from time stream data recorded from accelerated vibration testing and view its Fatigue Damage Spectrum (FDS) to understand the potential damage. Users can adjust the profile to reduce testing time.
- Max Number of Profile Points: 400
- Display: APS and FDS
- Options: low and high frequency at 1/24 octave max, target life and test duration.
The damage caused by accelerated vibration testing can originate from one of the following conditions:
- Damage caused by an extreme instantaneous stress on an object
- Damage caused by fatigue when high amount of a certain stress is applied to the object
FDS represents a spectrum with regard to the fatigue damage on an object. FDS function makes use of the S-N curve to construct the spectrum. The S-N curve represents the stress applied to a material (S) versus the number of cycles of applied stress. The S-N curve of aluminum is shown below:
Figure 1. S-N Curve of Aluminum
The FDS function helps reduce testing time by calculating the quickest path to destruction or damage. Testing time is accelerated by concentrating the random or swept sine energy, depending on the FDS calculation, to where it will induce the most fatigue damage.
In short, accelerated vibration testing with FDS helps the user understand which profile will cause more damage on the object and use this information along with other parameters such as kurtosis to reduce testing time.
Vibration Utilities App
Crystal Instruments in partnership with our sister shaker company Sentek Dynamics provides users with the Vibration Utilities mobile app on iOS and Android. This app provides calculation features for sizing your vibration profile (Random, Sine or Shock) and searches through our catalogue of shakers and controllers for the best fit.
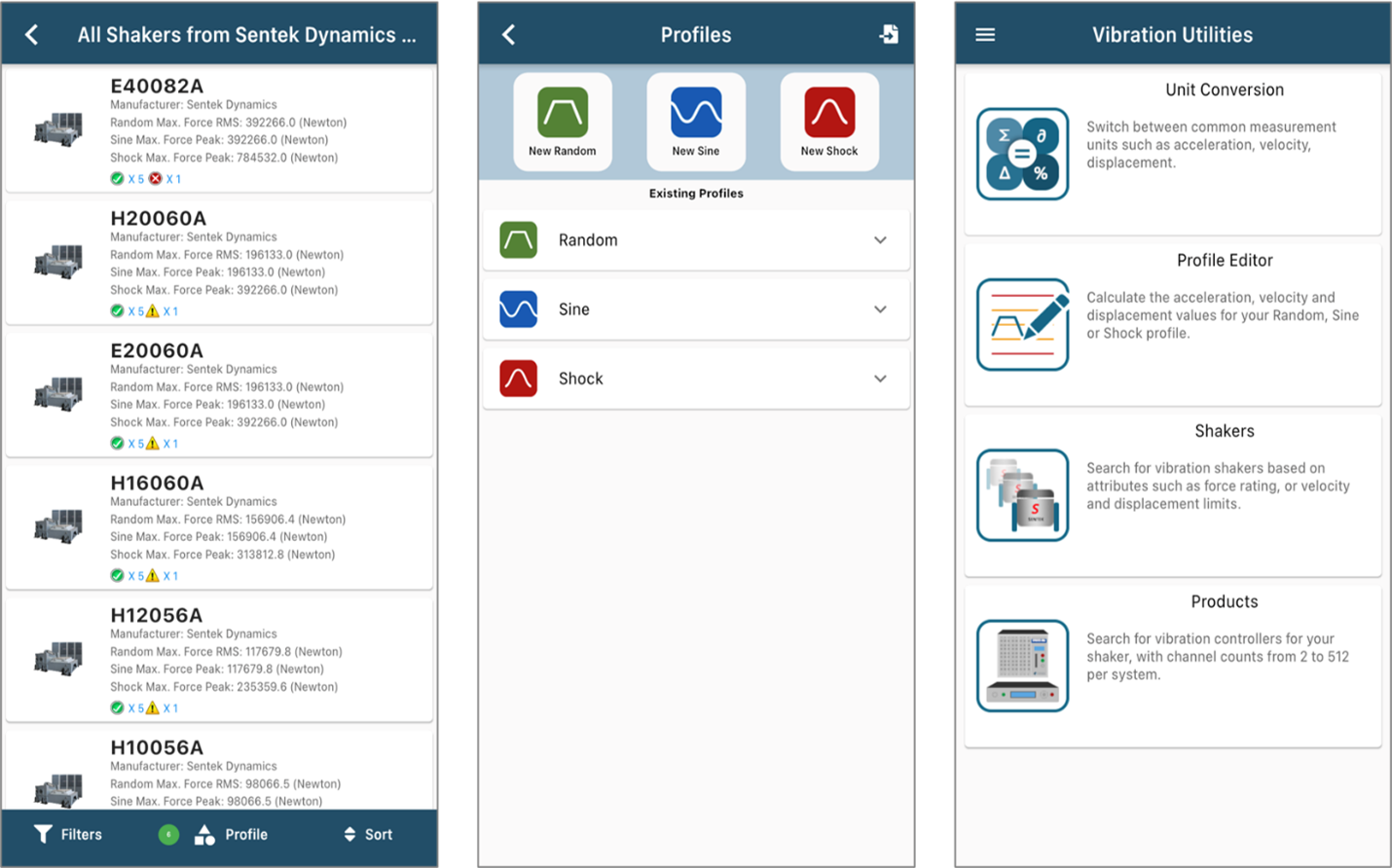


Continuous Data Recording
During accelerated vibration testing, all measurement input and drive signals can continuously record to a Spider-NAS or the internal storage residing in each front-end. Users can view and analyze data files with Crystal Instruments Post Analyzer. The variable sampling rate can be enabled to simultaneously record slow-change signals together with high speed vibration data.
Multi-Resolution for Random Vibration Testing
EDM provides the powerful multi-resolution feature that applies the selected resolution in the high-frequency range and 8 times of the resolution in the low-frequency range. The cut-off frequency, which divides the low and high-frequency range, is calculated by the software.
Accelerated Vibration Testing Hardware
- Spider-81/81B Accelerated Vibration Test Controller
- Spider-80Xi High Channel Vibration Test Controller - Scale up to 512 Channels
- Spider-80X Dynamic Measurement & Vibration Control System
- Spider-80M - MIMO Vibration Test Control System
Related Vibration Testing Software Options
- Random Vibration Testing
- Mixed Mode Vibration Testing
- Kurtosis Control for Vibration Testing
- Fatigue Damage Spectrum in Random Vibration Testing
Monitoring Through EDM Cloud
All tests in EDM-VCS support status checks through EDM Cloud. With EDM Cloud support, users can set up any vibration test to upload live data or run logs for completed tests to a cloud storage space provided by Crystal Instruments, where data is securely stored in the user’s account.
The EDM Cloud website is located at https://cloud.go-ci.com. Users can access EDM Cloud from anywhere in the world to check the status of past and current vibration tests. A secure login flow ensures the status can only be checked by authorized personnel with proper credentials. Multiple logins for accessing the same Cloud account is available.
|
|
|
|