Swept Sine Vibration Testing
Single Axis Shaker Vibration Testing
The Spider Swept Sine vibration testing system provides precise, real-time, multi-channel control using sine waveform. Swept Sine supports up to 512 input channels. Users can enable up to 128 channels for control and notching while designating the remaining as monitoring and time data recording channels. The recording option records time stream data at the full sample rate on all input channels, regardless of the total channel number. A unique hardware design provides a fast loop time of less than 10 ms. Black Box mode allows a user to operate the vibration test controller without a connected computer.
Swept Sine Control
Control Parameters
- Frequency Range: up to 46 kHz
- Sweeping Speed: Log (Oct/Min): 0.001 to 6000; Log (Dec/Min): 0.001 to 2000; Linear (Hz/Sec): 0.001 to 6000
- Sweep Rate Increment: Log (Oct/Min): 0.001 to 6; Log (Dec/Min): 0.001 to 2; Linear (Hz/Sec): 0.001 to 6
- Sweep Speed Control: Oct/Min, Hz/Sec, Dec/Min, Sweeps/Min, Sweep Time/Sweep, Cycles/Min
- Level Change: customizable in both logarithmic and linear rate
- Compression Rate: Fast (60 dB/S), Slow (20 dB/S), and Customized
- Spectrum Display Resolution: 256 to 4,096
- Loop Time: 10 ms typical
- Control Dynamic Range: 100 dB typical
- Measurement Strategy: Filter, RMS, Mean, Peak (multiple strategy allowed to each channel signal)
- Tracking Filters: Proportional: 7% – 100%; Fixed (Hz): 1 – 500 Hz
- Control Accuracy: ±1 dB through resonance with Q of 50 at 1 Oct/min
- Frequency Resolution: as fine as 0.000001 Hz
Notching and Limiting
Limiting is applied to control or monitor channels. Three types of limiting are available in Sine Control: frequency domain, time domain, and advanced limit. Two types of limiting are available in Multi-sine control: frequency domain and time domain.
Frequency domain limiting is spectrum limiting. Limit types are notching limit, abort limit, and alarm limit. Time domain limiting compares raw data or the RMS value of input channels to the high limit. The occurrence of exceeding the high limit is one of the system events to which desirable actions can be added. Advanced limit includes summed channel notching and vector notching.
A summed virtual channel is defined as the weighted average of raw time stream signals from multiple input channels. The Notch profile of a summed channel is defined in the frequency domain.
A vector RRS signal is defined as the vector sum of raw time stream signals from three input channels. The notch profile of a vector RRS signal is defined in the frequency domain as well.
Supports up to 128 notching/limiting channels out of 512 input channels.
Safety Features
- Abort Sensitivity: a single parameter allows the sensitivity and tolerance of various safety checks to be easily adjusted between customizable lower and upper bounds
- Shaker Safety Limits: limits for shaker acceleration, velocity, and displacement
- Open Loop Detection: open loop detection for control signal and each input channel. Detection is based on the pre-defined lowest allowed control level or maximum level change rate.
- Control Spectral Limits: spectral limits for the control signal
- Max Drive Limit: maximum voltage limit for drive output
Vibration Utilities App
Crystal Instruments in partnership with our sister shaker company Sentek Dynamics provides users with the Vibration Utilities mobile app on iOS and Android. This app provides calculation features for sizing your vibration profile (Random, Sine or Shock) and searches through our catalogue of shakers and controllers for the best fit.
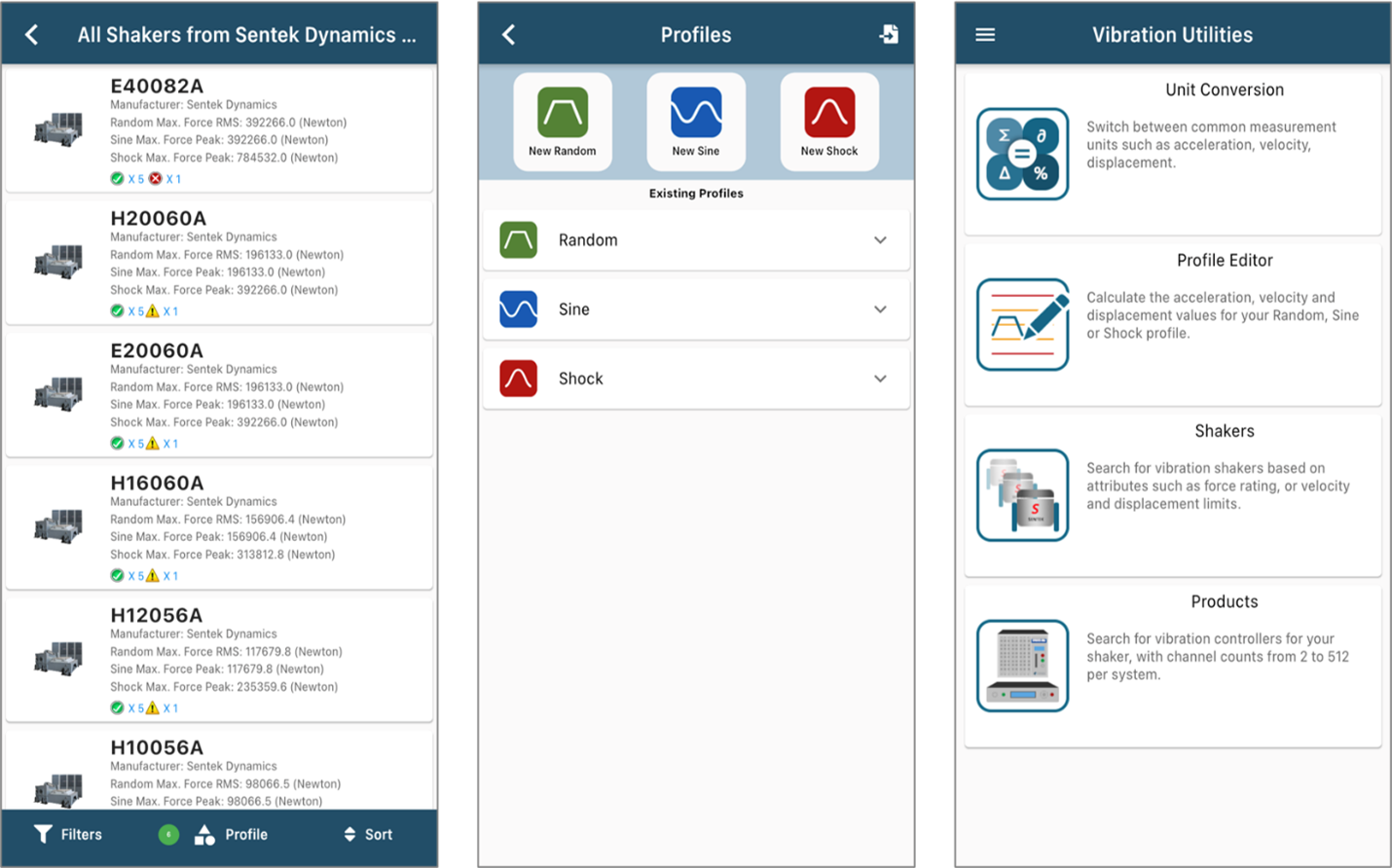


Continuous Data Recording
During vibration testing, all measurement input and drive signals can continuously record to a Spider-NAS or the internal storage residing in each front-end. Users can view and analyze data files with Crystal Instruments Post Analyzer. The variable sampling rate can be enabled to simultaneously record slow-change signals together with high speed vibration data.
Unique Features in Swept Sine Vibration Testing
Vibration Visualization: The EDM Vibration Visualization feature is available in EDM VCS software all test types, including MIMO VCS. This option provides fast and efficient structural model generation and full 3D visualization of the online vibration pattern on the structure under test.
Multiple instances of EDM VCS can run simultaneously on the same computer. Each instance connects a Spider system to run the vibration controller software. All instances must run different tests. This feature provides a central place to control multiple Spider systems and perform vibration tests separately.
Black Box Mode: Operating Without a PC
A supported front-end can operate in Black Box mode which allows it to perform a test without a connected PC. In this mode, a PC is used only to configure the system before the test and then to download the data after the test is complete.
Multi-shaker control (MSC) is a unique feature offered enables users to view and monitor multiple shaker tests from one PC station. Up to 12 controllers can be accessed simultaneously.
Spider Vibration Testing Hardware
A Spider system can consist of one or more Spider hardware front-ends. The user constructs the system by combining Spider front-ends detected on the same LAN. The software validates and displays hardware attributes of each Spider front-end. The following hardware is supported by EDM VCS software for vibration control, monitoring, and data acquisition.
- Spider-81/81B Premium Vibration Test Controller
- Spider-80Xi High Channel Vibration Test Controller - Scale up to 512 Channels
- Spider-80X Dynamic Measurement & Vibration Control System
- Spider-80M MIMO Vibration Control System
- Spider-80SG General Data Acquisition Device with Strain Measurement
Related Vibration Testing Software Options
- Resonance Search and Tracked Dwell (RSTD) Vibration Testing
- Multi-Sine Vibration Testing
- Total Harmonic Distortion (THD) Measurement for Sine for Vibration Testing
- Sine Oscillator
Monitoring Through EDM Cloud
All vibration tests in EDM-VCS support status checks through EDM Cloud. With EDM Cloud support, users can set up any VCS test to upload live data or run logs for completed tests to a cloud storage space provided by Crystal Instruments, where data is securely stored in the user’s account.
The EDM Cloud website is located at https://cloud.go-ci.com. Users can access EDM Cloud from anywhere in the world to check the status of past and current tests. A secure login flow ensures the status can only be checked by authorized personnel with proper credentials. Multiple logins for accessing the same Cloud account is available.
|
|
|
|